As a power source for our industry, hydrogen offers vast potential.
But several obstacles remain. We look at the challenges and opportunities.
When it comes to using hydrogen as a source for powering vehicles – including cranes – there are currently two main development streams under research.
The first is to use hydrogen as a direct fuel, typically in combination with a diesel-combustion engine. This solution can help to reduce location emissions and thus – in a given context – may be more sustainable than existing alternatives.
The other development stream concerns fuel cells. These are more eco-efficient and cheaper to operate than combustion engines, making them an attractive solution for day-to-day operation of cranes and other machines used in ports. The issue with fuel cells is that they’re expensive. The initial capital outlay is high.
“It’s still unclear which of these two technologies will emerge as the leading one in our industry. Perhaps both will,” says Tuomo Korkeaviita, Offer Manager RTG Cranes at Konecranes.
“We already see huge investment from the automotive industry in both of the streams. For example, Toyota brought the combustion engine back to create the hydrogen-combustion engine, while there are also cars available that run purely on fuel cells.”
“Our expectation is that there are already commercially available hydrogen-combustion engines we could use in our industry. We are also expecting that fuel cells will be available in a couple of years,” says Korkeaviita.
Converting Konecranes RTGs to hydrogen hybrids?
Konecranes already offers a wide range of flexible power solutions for our RTGs (Rubber Tired Gantry cranes). These include our Hybrid Power Pack, which turns a fully diesel RTG into a diesel-electric hybrid. We also offer fully electric Cable Reels and Busbars, and battery-driven RTGs. All these options give our customers flexibility to choose the power option best for their business and environmental goals.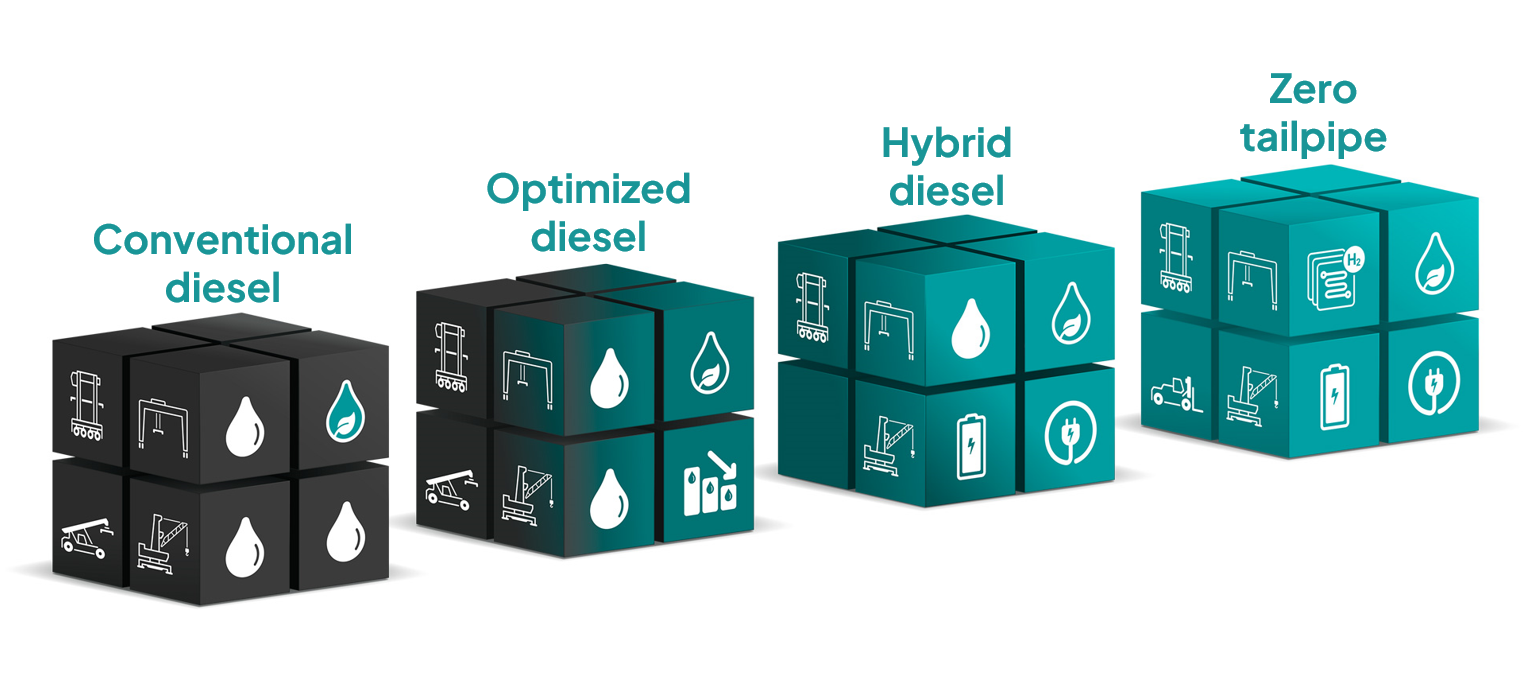
The relevance to using hydrogen as a fuel source – in combination with a combustion engine – is that Konecranes already has experience of successfully running hybrid-engine models (with electric power packs). Now it’s just a question of getting hydrogen engines up to speed so they can replace electricity.
In fact, Volvo has already introduced a dual diesel-hydrogen engine, including full redundancy . When hydrogen is not available, the engine simply switches over to diesel. In another significant industry development, engine-leader Cummins has introduced a 15-litre hydrogen engine paired with an internal combustion engine.
“We know that when the Cummins diesel engine is paired with the hydrogen, then the horsepower is reduced to about 300. But there would be no need to make a double-sized engine for a Konecranes RTG, as we already have the battery technology from the diesel hybrid,” explains Korkeaviita.
“You can just keep the same size combustion engine and use it to charge the batteries as the main source of power for the crane. This gives you the flexibility of a diesel RTG and the efficiency of a hybrid RTG – except it would be charged with hydrogen instead of electricity.”
“When there are 110 or 120 kilovolt ampere fuel-cells available, you’ll be able to do the same with a fuel-cell hybrid,” he envisions.
Bringing hydrogen production to the terminal
There is also a third possible future for hydrogen in the lifting industry: generating it at the terminal itself as a local power source.
“Why not completely get rid of the diesel, put batteries in the cranes, and charge these batteries using locally produced hydrogen? We already know that RTGs spend up to 40% of their time idling, so just send them to the charger during that time. Less than eight minutes of charging gets you one hour of operation,” explains Korkeaviita.
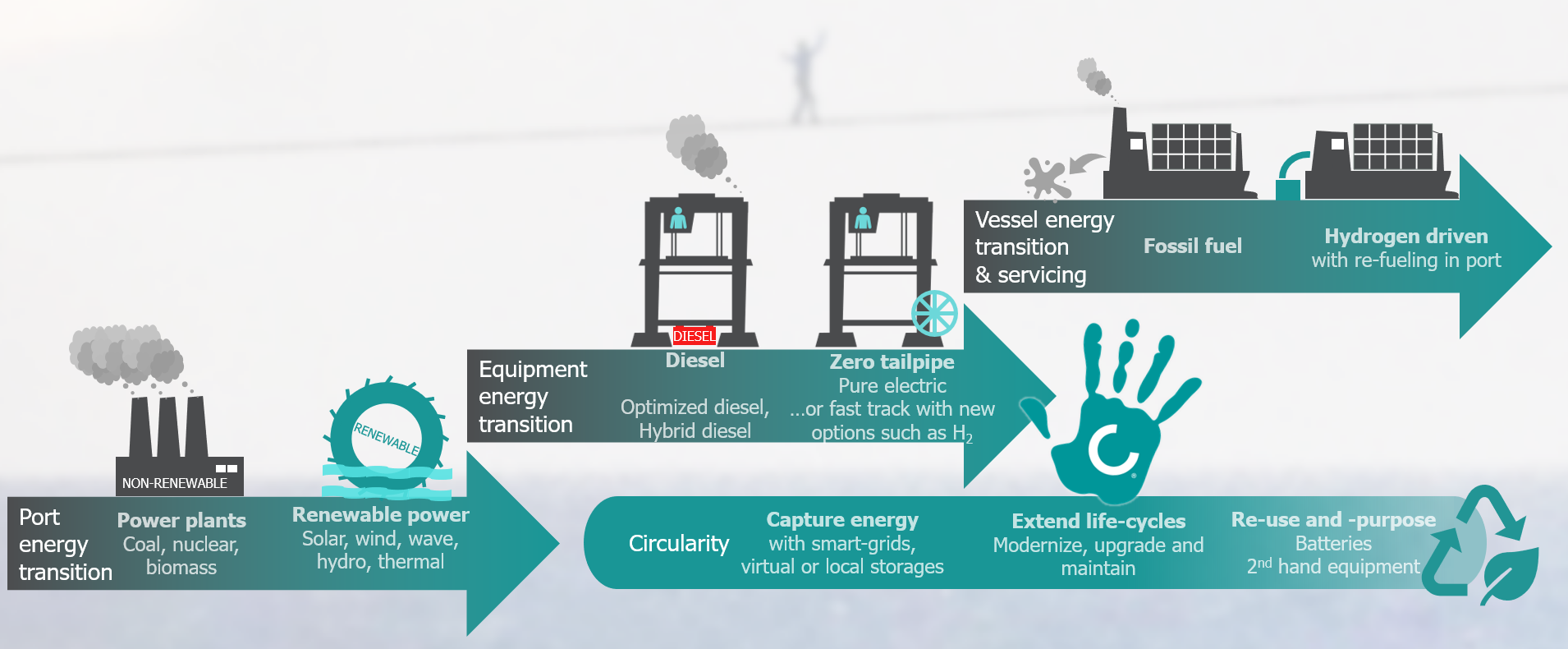
This scenario for the future is not as far-fetched as it may sound. Many port and vessel operators are already taking the sustainability step of building dock-side biomass power plants to generate biofuel. These local plants can also be used to produce and store hydrogen. The hydrogen can then be used not only for dockside lifting equipment, but also sold to shipping companies to power their seafaring vessels.
“It’s another way for port operators to be part of the green corridor and help to move the broader industry further towards sustainability,” envisions Korkeaviita. “We don't yet know if or when hydrogen will become available as a viable option. But if it does, it will certainly be our industry’s fast track to zero emissions.”
Konecranes works for a decarbonized and circular world for customers and society. We are helping to build the means to get there for our customers, step by step. At Konecranes Port Solutions we call this Ecolifting™: a systematic movement towards lower CO2 per container move. Today, all Konecranes factories globally use renewable electricity and we are committed to cutting our global emissions in half by 2030.
Related materials